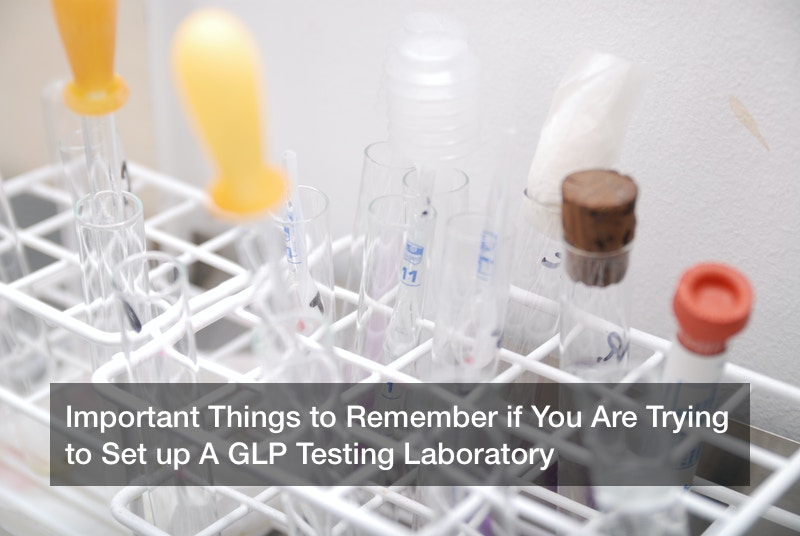

For people all over the country, drug development and manufacturing companies do a lot of good by providing life-saving medication and medical aid that can prove to be crucial in providing relief for a number of diseases and health concerns. If you run or manage a company operating in this industry, there can be quite a few things that you would need to accomplish in your drug development and manufacturing facilities to truly make them ready for the kind of work that you are looking to do. In connection to this, there can be a number of standards and compliances that you would have to get in order first.
Drug development laboratories and manufacturing facilities require a very specific set of parameters to be strictly enforced due to health and safety reasons and various other factors. These have to do with the interior conditions of these facilities, things that can directly influence the outcomes of the procedures inside. Failure to maintain these conditions can adversely impact the procedures being run in these facilities, can lead to major health and safety hazards, and can make progress a lot more difficult for your business. There can also be a number of compliance issues that you would have to get right in order to operate freely in this industry.
This is where clean room standards, GMP standards, GLP standards can really matter. These recommend a set of parameters of conditions that you would need to strictly enforce in your drug development laboratories and manufacturing facilities in order to remain compliant with government regulations and have the best chance of achieving your goals with product development. Building a clean room or a GLP testing laboratory is by no means an easy task. There is a lot that needs to be assessed, mitigated, and controlled precisely before you can reach the exacting standards of these norms.
To achieve GMP storage conditions or to build a GLP testing laboratory, you would first need to have complete knowledge about the parameters involved in the process. You would need to research methods and means in order to have granular control over temperature and humidity levels inside these facilities, along with failsafe measures and constant monitoring. You would need to have in place equipment and sensors that can maintain attributes like temperature, humidity, and air quality in these facilities and have measures built into the place that can tackle emergency situations. The tolerance levels can be extremely low and there is very little margin of error to play with here.
For example, you would need to restrict the entry of particulate matter in clean rooms to an exacting standard. Through the use of fume hoods and air quality sensors, you would have to keep the particulate matter to a minimum to ensure that the room functions as intended. Similarly, A GLP testing laboratory would need to adhere to GLP or good laboratory practices that have specifications and recommendations regarding the right laboratory and safety equipment to use, the right clothing and tools to use, the right interior conditions to maintain. GMP standards can apply to manufacturing facilities the same way.
Keeping all this in mind, it can be a good idea to start looking at professional companies that can help you with these best practices and enlist their help in order to build clean rooms and GLP testing laboratories. Not only would getting this professional assistance make it easier to achieve these exacting standards in your clean rooms and GLP testing laboratory, but it would also make it easier to maintain those standards over time through regular assessment and inspection of all the equipment and techniques involved in maintaining those conditions. With the right processes, checks, and balances in place, you can have the peace of mind that can only come from knowing that you are perfectly compliant with all regulations and best practices that apply to your business.